Prefabricated modular condos can help address Toronto's housing shortage, builders say
Shift in the construction industry long overdue, experts say
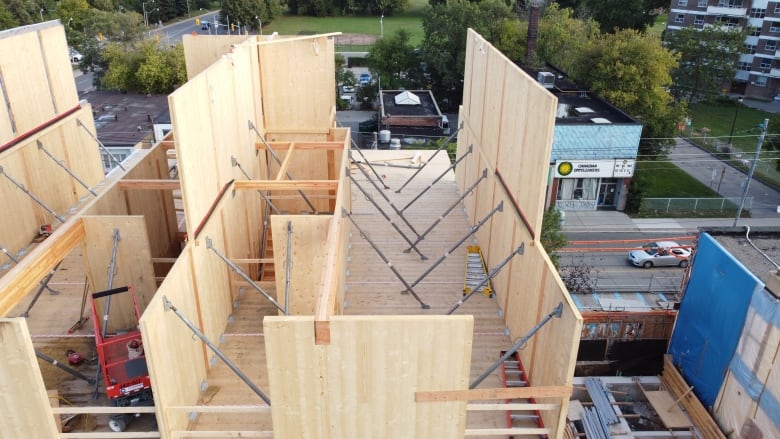
People searching for an affordable home in Toronto could soon have a choice never seen before in Canada's largest city: prefabricated modular condos.
Inspired by a style of building found in parts of Scandinavia, Germany and elsewhere in Europe, a trio of companies is hoping to construct three mid-rise condo buildings and do so quickly and sustainably, says Michael Barker, co-founder of R-Hauz Solutions, a firm that builds prefabricated homes.
"The traditional way of construction is flawed. It failed," said Barker. "It's too intensive … There's a lot of waste on labour, a lot of mistakes get made, things get dragged out."
The companies are seeking the city's approval for the project as the Toronto area grapples with an affordable housing crisis partly due to what urban planners call "the missing middle" — a lack of low- and mid-rise multi-family buildings. Advocates say many proposed housing projects are slow to launch or don't get off the ground due to complex rules, as well as the time and the expense of construction.
This new approach, called a "flat pack modular strategy," would solve those problems partly by being faster and cheaper — delivering a building like "a house of cards" where the pieces come from the factory ready to go and teams just assemble them on the site, Barker says.
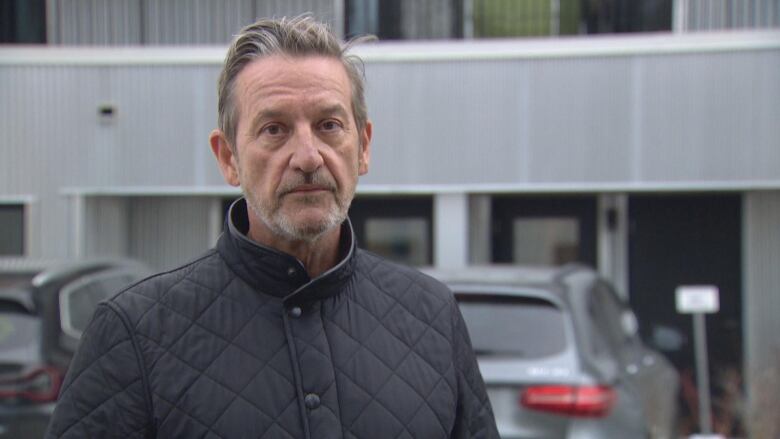
He and his partners, Windmill Developments and Leader Lane Developments, are planning to construct the three condo buildings in the city's west end near the Mimico GO Station, with 83 suites in all. The developers say they hope to start the presale of units in August and begin building by December.
The strategy will allow the developers to work much faster, Barker says. Until now, six-storey mid-rise homes have often been just as complicated to build as larger structures, creating little incentive to pursue these developments, he adds.
The case for a new way of construction
R-Hauz Solutions finished an apartment building on Queen Street East in Leslieville last summer that is now occupied. The condo buildings they're planning to construct as part of this plan will essentially be copies of that project, says Barker.
They'll construct the buildings with Ontario cross laminated timber (CLT), which "sequesters carbon" for life, he says, adding that the method also minimizes the use of concrete, a material he says is worse for the environment.
Under this method, the weather doesn't slow construction down as much and working conditions will usually be better, says Tamer El-Diraby, a civil engineering professor at the University of Toronto who isn't affiliated with the project.
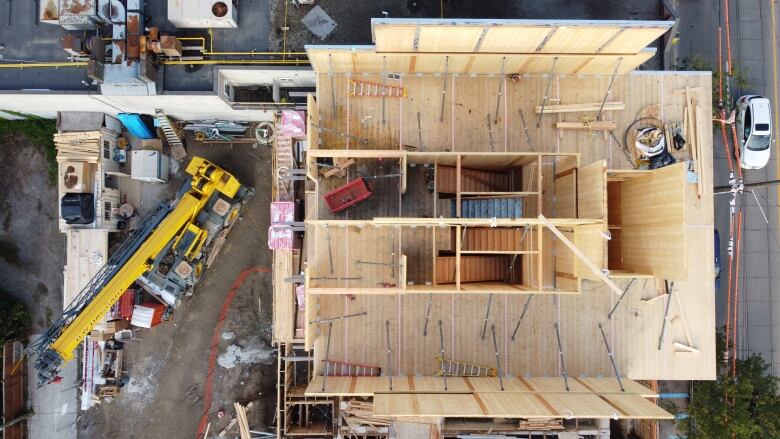
He also says it will be easier and cheaper to recruit and teach workers to build these prefabricated structures than with more conventional construction methods.
"Finding people who are trained and willing to go to the site is becoming harder and harder," El-Diraby said. "And the cost of that is increasing."
The new method may provide more jobs in the construction industry for young people, women and those with technical interests, he says. There are also advantages for the neighbours. It means less noise and dust and fewer disruptions because the project gets finished more quickly, El-Diraby says.
'Compressed timeframe'
There are also efficiencies in the planning process, says Don Manlapaz, a partner at Leader Lane Developments.
"It's such a compressed timeframe," said Manlapaz, "You'll be able to move in in two years."
And because the three condo buildings are using the same prototype, blueprint and building design, the approvals process can be streamlined.
"Instead of having three separate development approvals in a development vision, it's one vision ... reviewed in a collection," he said.
He says a more modest low- or mid-rise project like this one that fits in with the existing neighbourhood can undergo a shorter approval process at city hall, with no need for zoning bylaw amendments, something that can often be time consuming with other construction projects.
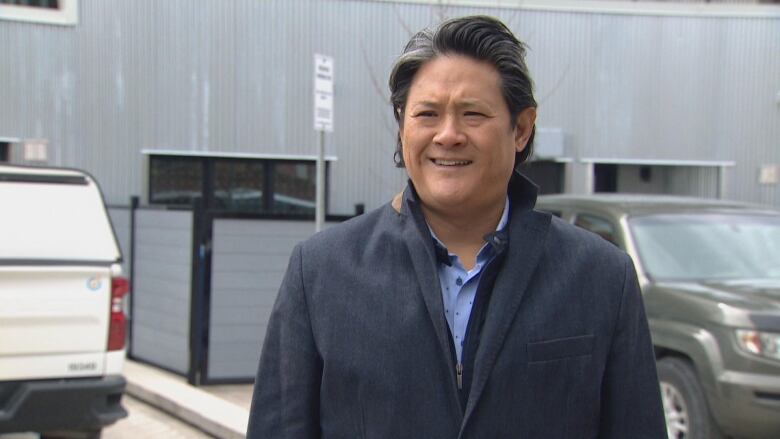
Experts say the shift is a long time coming.
"Largely speaking, prefab and modular architecture is lagging in the industry," said Jason Halter, a professor at the Daniels Faculty of Architecture and Design at the University of Toronto.
He sees positives for sustainability and construction speed, noting even reducing continuous travel to a site by several months could be significant for saving energy and time. There also tends to be fewer materials wasted due to on-site errors, he says.
Not cheaper… yet
But Halter says: "I've yet to see a prefabricated building be lots less expensive as the claim might be."
El-Diraby agrees, saying like any new technology, it might not save money right away.
"The scale matters a lot in this regard," he said.
While the partnership has only three condo buildings in the works right now, R-Hauz Solutions can sell their product to other developers, said Jonathan Westeinde, CEO and founder of Windmill Developments.
Halter says he hopes some of the savings from building prefabricated and modular housing efficiently, sustainably and at a lesser cost end up in would-be home owners' wallets.
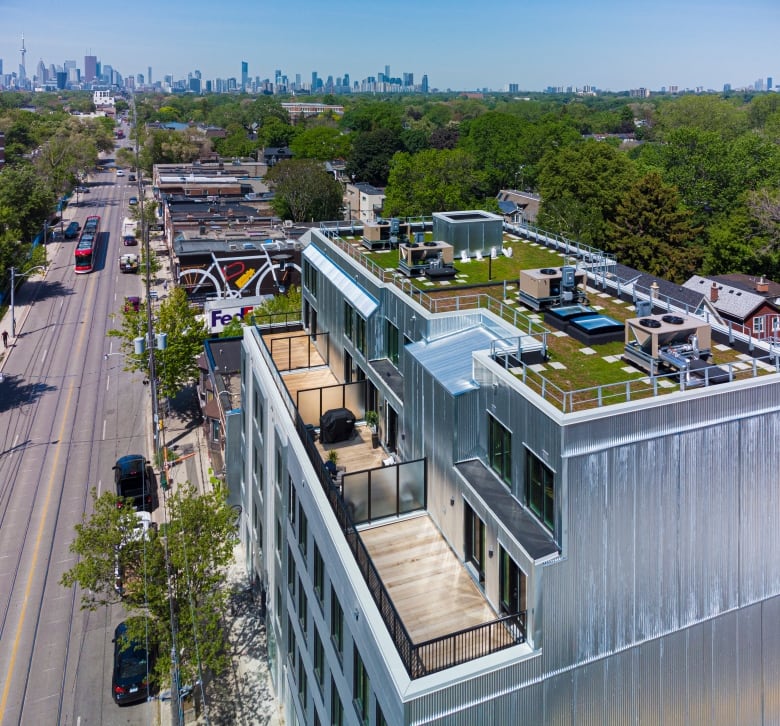
"It would be unfortunate if a developer were to maximize their profit in terms of their construction application and not pass on some of those savings."
The initial three mid-rise condos would be cheaper than most other street-level options like townhouses, but roughly comparable to prices in large towers, says Westeinde.
Windmill has other projects in the works with an affordable housing component and hopes as companies create models for working in this new way, it becomes easier to replicate and cheaper, he says.
"We think [it] has a real potential for a long-term program to sort of fill that missing middle," he said.