Is mass timber the next big thing in cheaper, greener construction? More provinces are saying yes
The material is touted as a way to quickly build more housing, but some builders think it's still too unproven
Urban downtowns are sometimes called concrete jungles because the apartments and office buildings that make up skylines from New York to Vancouver are generally made of — what else? — concrete.
But that could change with a push underway to build more tall buildings with another material: mass timber.
Mass timber is an umbrella category of materials made by binding layers of wood together to create larger, stronger elements like panels and beams. Proponents say it's faster and easier to build with than concrete and steel, and less carbon-intensive to boot.
If concrete and steel are the Coke and Pepsi of highrise construction, mass timber has so far been more of a generic-brand cola. Mass timber made up just one per cent of all building construction materials in North America in 2022, according to an RBC report.
But analysts expect the market to rapidly expand in the years ahead, and all across the country, existing mass-timber plants are being expanded and new ones are in the works, from B.C. and Alberta to Ontario and Nova Scotia.
"The demand is extremely high for mass timber now," said Frank Gannon, director of stakeholder engagement with mass timber manufacturer Western Archrib. He spoke with CBC News inside a new, 155,000 sq. ft. facility the company is building north of Edmonton to keep up with its growing orders.
"We are filling capacity slots about 10 months out from today — so yes, the phone's ringing off the hook."
The industry is getting a boost from new building codes that allow taller mass-timber buildings, and federal and provincial programs and policies that encourage builders to use more of it.
But so far, the uptake of mass timber has been uneven across the country, as some builders remain reluctant to switch from tried-and-true materials to something new.
And while much of the buzz around mass timber comes from its low carbon profile, some experts disagree about how climate-friendly it really is.
Beams and columns, floors and walls
The two most common types of mass timber are glue-laminated timber, or glulam, and cross-laminated timber, or CLT.
Glulam, which has been around since the early 20th century, is used to make beams and columns. CLT panels are a more recent innovation used for floors, roofs and walls.
Taken together, the two materials can serve as an alternative to concrete and steel in a building, said Brian Merwin, senior-vice president with Mercer Mass Timber in Vancouver.
"CLT is the transformational material for tall buildings," he said, adding that most of the material used in highrises is for the floors. "[It's] sort of filled that missing gap to get us to where we are today."
Federal tracking shows mass timber has most commonly been used in institutional buildings, like schools and community centres, but as more research has emerged attesting to the fire safety of tall wood structures, recent changes to building codes have opened the door to building higher.
In 2020, the National Building Code of Canada was changed to allow encapsulated mass-timber construction up to 12 storeys. That means mass timber components in these taller buildings have to be covered by a fire-resistant material, like drywall.
Ontario and B.C. have gone further, and will allow up to 18-storey buildings.
Faster and lighter
Building with mass timber carries several advantages, according to structural engineer Robert Malczyk. It's faster to work with than concrete, he said, because panels can be largely prefabricated and assembled on-site.
His own five-storey Vancouver office building, made with mass timber, was erected in 12 days.
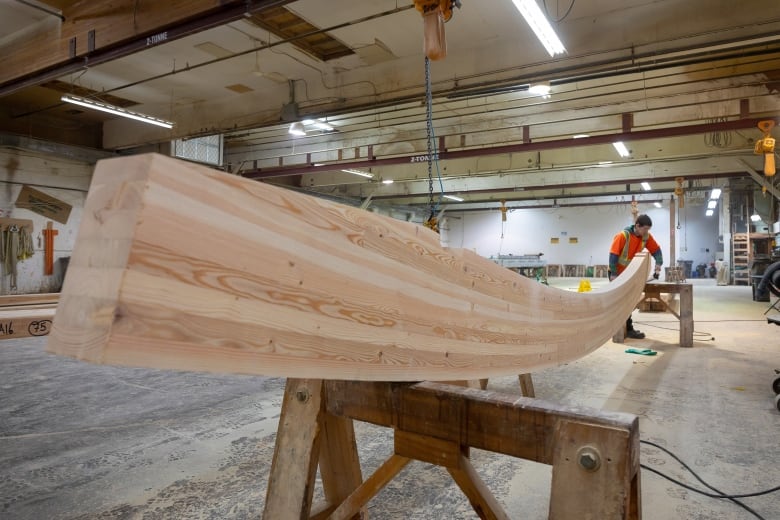
"As an owner, I saved a lot in crane time, in closure of the streets time," said Malczyk, principal with the Timber Engineering consulting group.
Mass timber is also relatively light, making it more resilient to earthquakes, he said. Plus, many people simply like the way it looks.
"It has this beautiful calming effect, it's a natural material. We just love to be surrounded by wood."
Proponents of mass-timber construction also point to its environmental advantages.
Wood is a renewable resource, said Mohammad Mohammad, a senior research adviser with Natural Resources Canada, and producing it generates far less carbon compared to steel and concrete.
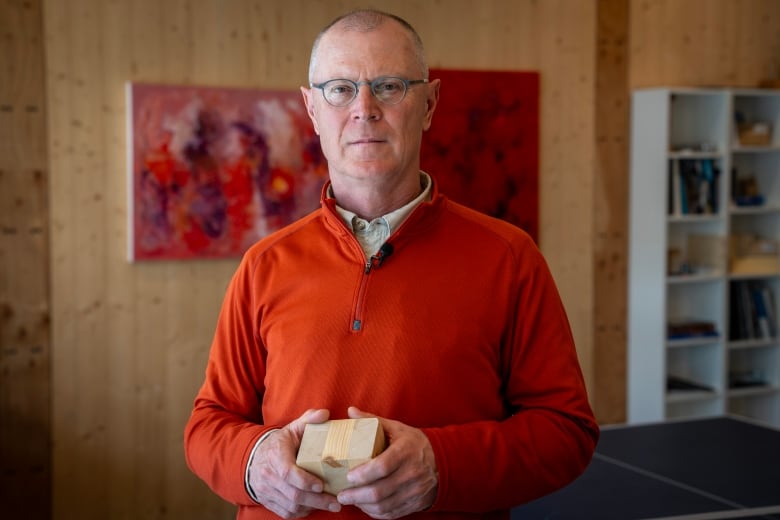
At the end of a building's lifespan, he said, wood can also be recycled or reused, rather than being sent to a landfill.
"It has a lot of environmental benefits," said Mohammad, who works with a federal program funding innovative wood-construction projects that is so oversubscribed, its website contains a high-volume notice.
Green claims questioned
Not everyone is ready to throw out their cement mixers and switch to mass timber.
While construction in B.C. and Quebec, for example, has grown thanks to "wood-first" policies in their respective provinces, other provinces remain a bit more hesitant.
Many developers in Alberta, for example, are studying mass timber carefully but haven't yet felt comfortable green-lighting a mass-timber residential building, said Scott Fash, CEO of BILD Alberta.
"I think we're in the phase of exploration and not quite action," he said.
Insurance premiums can also be high for builders working with mass timber, said analyst Sean Steuart, not because it's a more dangerous material but because it's so new.
"It's just not a well established industry, and as such, the insurance-underwriting framework is not as well developed," said Steuart, director of equity research with TD Cowen.
He said there's also a mismatch between supply and demand of mass timber: most demand is coming from Eastern Canada but manufacturing is concentrated in the West, which can drive up shipping costs.
Another risk: not everyone thinks mass timber is as sustainable as it's made out to be, and some experts caution against cutting down more trees to build with more mass timber.
"The most valuable thing we can do with forests is to leave them standing and growing," said Timothy Searchinger, whose work on mass timber has been published in the journal Nature and by the World Resources Institute.
He suggests the world would be better off exploring more low-carbon concrete options instead.
Faster housing construction?
Mohammad, with Natural Resources Canada, said the vast majority of forests harvested in Canada are sustainable, and that usually more than one tree is planted for every one that's cut.
As Canada attempts to rapidly ramp up housing construction in the years ahead, he believes mass timber will play an important role in the overall mix of construction materials — especially in Northern communities, where concrete can be prohibitively expensive and hard to ship.
"[You can] basically establish a new housing development within weeks or months," he said.
"Now that we are able to go taller and larger with mass timber, it's just adding another construction system, another tool to our toolbox."
Rick Jeffery, CEO of the Canadian Wood Council, doesn't see a scenario where mass timber fully replaces concrete and steel. He also pointed out that it's not common for buildings to be made of mass timber alone: typically they're made of some mix of the three materials.
But he believes mass timber will be used much more often as Canada aims to build its way out of the housing crisis (a goal that will require another 3.5 million homes by decade's end).
"We see there's a big opportunity on that residential side."