How the COVID-19 semiconductor shortage has brought Canada's car industry to a halt — again
Semiconductor microchips are the toilet paper of 2021 — and a lack of them is holding up production
Even before the pandemic, 2020 was always going to be an uncertain year for Canada's automotive industry.
The Big 3 automakers — General Motors, Ford and Chrysler (now known as Stellantis) — were set to negotiate multi-year work agreements with their main unions, after the previous agreements with their workers had expired.
Then COVID-19 hit, and everything changed. Buyers weren't coming to showrooms for fear of getting sick, so sales slowed to a crawl. Factories shut down to keep workers safe.
By the time consumers felt safe enough to take their first tentative steps back into dealerships this year, they were confronted by a new problem: There were no cars to buy.
That's because when things slowed down in 2020, car companies slashed their orders from their suppliers for the components that go into them. When demand came roaring back, those same suppliers could not ramp up fast enough, especially the makers of the cheap little semiconductor microchips that are in just about everything these days.
"Automakers in Canada initially thought that demand would be very slow recovery over the course of the pandemic, so they cut their chip orders," said Rebekah Young, an economist with Scotiabank.
It's not just the car companies, either. Makers of everything from iPhones, to gaming consoles and even refrigerators can't find microchips right now, which is a global supply crunch for just about everything.
A typical car rolling off the line today likely contains dozens of semiconductor microchips that control everything from the headlights to the entertainment system to GPS navigation.
They're relatively inexpensive, adding a few dollars apiece to the cost of a typical car. But they're also highly customized, which means it's next to impossible to find alternatives on short notice. But without that custom-made $1 microchip, a car company can't finish a car that might sell for $40,000 — and the industry is scrambling to get its hands on what's available.
"Do you remember the toilet paper shortage in March and April of 2020?" automotive journalist Stephanie Wallcraft said in an interview. "That's pretty much what we're going through right now in terms of semiconductors."
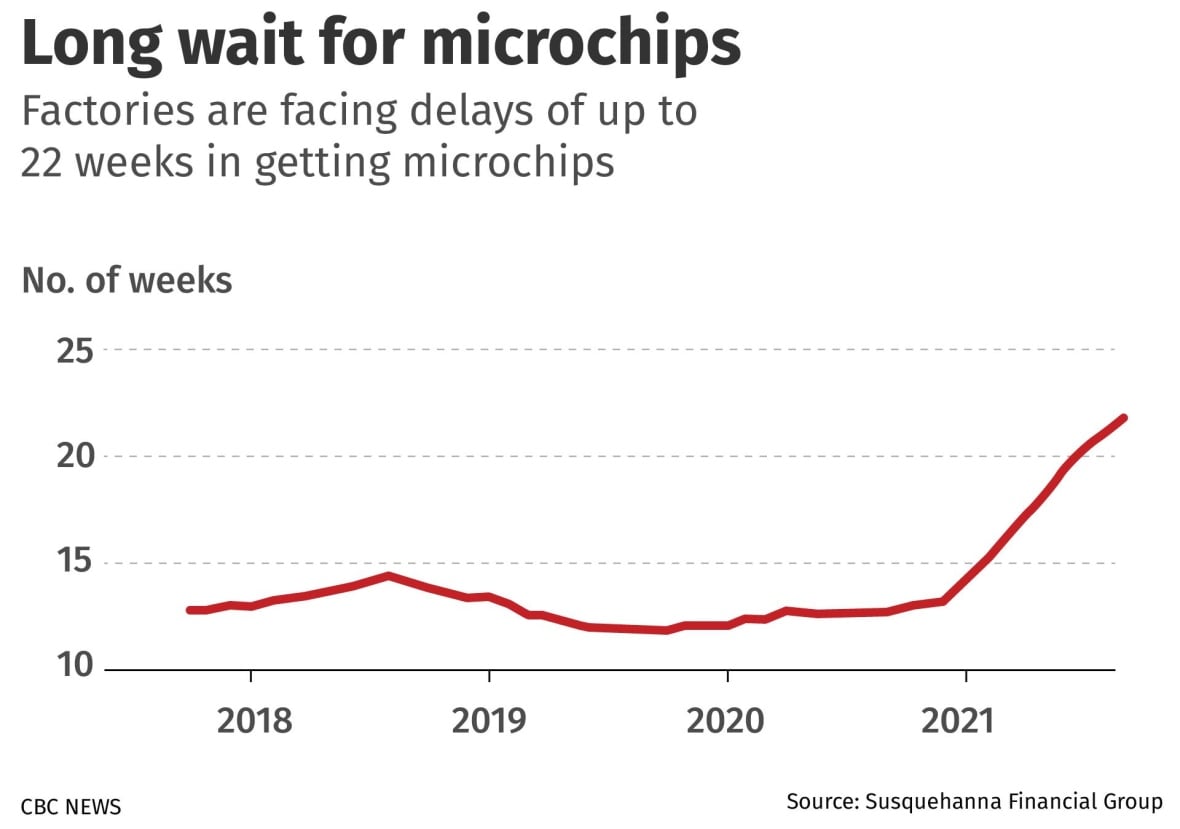
"Everybody's trying to get semiconductors all at once and there's just not the supply to get that inventory out," she said.
Car companies aren't necessarily at the front of the line, so they're waiting their turn same as everyone else. That's causing them to idle factories in Canada until they can get the components to start building again.
GM's facility in Ingersoll has been down for most of the year, and Ford's main Oakville plant has been idled at times, too. The Stellantis facility in Windsor was offline for two months up until May before it reopened at limited capacity.
As recently as last year Stellantis was floating the idea of expanding production there but this week the company waylaid staff with news that it would be closing one line entirely and laying off 1,800 workers.
In the labour deals they hammered out late last year, Canada's big car makers made it clear that the future of the automotive industry in Canada will be in making electric vehicles, but most of those won't be rolling off the lines until some time in 2024 at the earliest.
Until then, Canadian car plants don't have a lot to do, and a big part of the problem is that the vehicles Canadian plants are set up to make aren't the ones that are selling.
"What they're doing is they're allocating the minimum chips to their most profitable vehicles," Unifor president Jerry Dias said in an interview with CBC News.
"If you're looking at the industry in North America that would be predominantly pickup trucks and SUVs."
Young, the economist, says Canada is on track to produce about 1.2 million vehicles this year. That would be the lowest annual total since 1982 — below the 1.4 million the country made in pandemic-stricken 2020, and well off the 2.2 million annual pace that the country had been cranking out for the decade leading up to 2019.
Chip makers, mostly in Asia had been ramping up production through the first part of 2021, before the delta variant put a chill on everything again. Malaysia makes about one seventh of the world's semiconductors, and factories there have been idled for September and October. Vietnam is another major supplier, and they too are about three months behind because of COVID lockdowns.
For both car buyers and the people who make them, the good news is that the experts think things will get back to normal at some point. But the bad news is it could take a while.
"Demand for vehicles is very strong this year, and that could have easily closed pre-pandemic gaps this year if there were enough vehicles to buy," Young said.
But without enough chips to go around "we see that being pushed out not only to 2022, but in fact 2023."