Company aims to remould plastics industry with nano-crystalline cellulose from trees
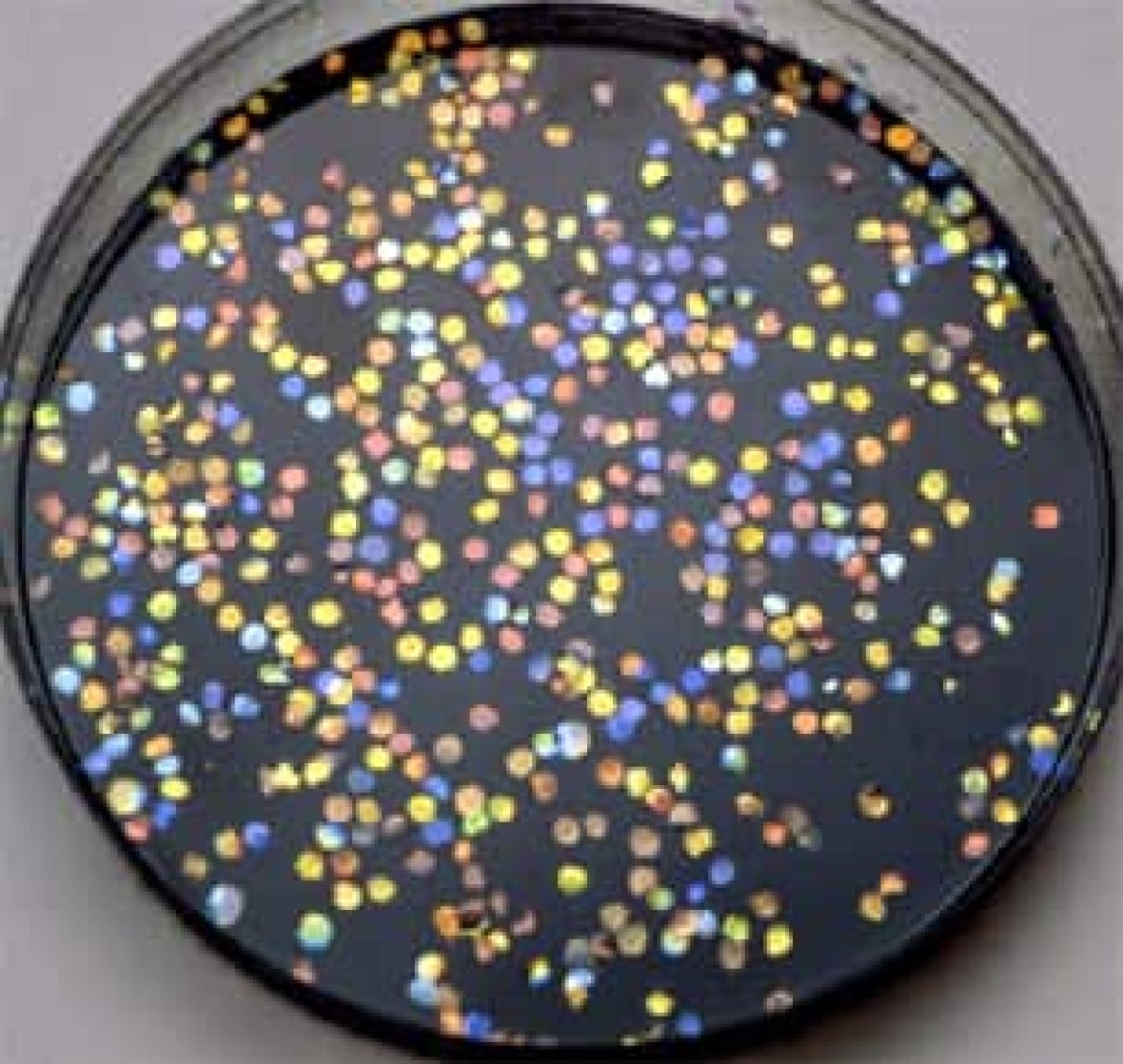
Cinema buffs will recall the quirky, uncool character in the 1967 movie The Graduate who proselytized to Dustin Hoffman's character about the huge opportunities in the plastics industry.
Today, Canadian scientists are betting that the future of plastics involves replacing them with sustainable materials made from trees.
Faster cars, compostable plastics, ultra-hard iridescent coatings: these are some of the potential uses of nano-crystalline cellulose (NCC). It's a new material produced from wood cellulose, using a cost-effective method developed by researchers at FP Innovations, a non-profit forest industry research consortium based in Montreal.
NCC has many unusual properties, in addition to having all the biodegradable attributes associated with its plant-based source.
Materials scientists are in awe of NCC's extraordinary potential — among its many attributes, it's strong, lightweight, can conduct light and electricity, has anti-microbial properties, can be embedded safely in body tissue, and even has self-cleaning characteristics. In toxicity tests conducted for Environment Canada, NCC was found to be environmentally benign and no more toxic than salt.
And it has a pleasing iridescence.
Cellulose
FP Innovations has also recently started working on a new project to produce bio-plastic from tree and plant cellulose instead of food crops.
Most of the recent bio-plastics developed by major chemicals companies are made from three major food sources: Glucose derived from corn starch and sugar cane, and oils from soya beans, says Crawford.
"Many environmentalists say bio-plastics shouldn't compete with food resources. The same arguments against ethanol apply to bio-plastics," says Michael Paice, principal scientist in charge of the new project at FP Innovations.
But cellulose-based bio-plastics research is still in the early stages. Unlike NCC, scientists have yet to find a viable process for producing large quantities economically, says Paice. It's a more difficult process, as cellulose from trees or other plant sources must be converted into glucose, which bacteria then convert into bio-plastic granules stored within their cells.
"To get from cellulose to glucose that can then be used by bacteria is not easy. It's a challenge to do that cost-effectively," says Paice.
Nevertheless, Paice believes forestry researchers will eventually find an efficient way to make bio-plastic from waste cellulose produced by pulp and paper mills when processing trees, which would be a cheaper and more ethical source than food crops.
"Over time, we'll see more bio-plastic production from non-food sources, but for now, the technology is there to make them from corn and soybean cost-effectively," says Crawford.
Major chemical companies are also looking for alternative non-food sources for bio-plastics. In addition to ethical issues, there are also economic incentives. Current bio-plastics are two to three times more expensive than conventional plastics. The high costs are slowing their uptake, says Crawford.
Although demand for bio-plastic is still relatively small today, that may change soon, he adds.
"Cargill's biggest single customer is Wal-Mart, which has advised all its suppliers it wants them to use more environmentally responsible packaging. And in Europe, Cargill has said it will build a big plant there if five to 10 major retailers get together and do the same. This will all drive more demand, which will help scale up production of bio-plastic and bring costs down," says Crawford.
"When NCC is applied in layers on a surface, it can change colour with the angle, like a bird's plumage," says Dr. Richard Berry, lead scientist and co-ordinator of the nanotechnology initiative at FP Innovations. Materials can be made in various colours without the use of dyes and chemicals.
"NCC is beautiful," says Orlando Rojas, chair of the American Chemical Society.
Commercializing NCC
Although the concept of NCC has been around for decades and its source is abundant, producing it has been an expensive proposition.
The use of NCC in everyday products isn't a distant, theoretical possibility. Berry and his team have developed a process that they say can produce large-scale quantities economically.
Designs for the construction of a one-ton-a-day production facility have been completed by Vancouver-based NORAM Engineering, and the site will be announced early next year. The plant will start production in 2011.
A wide range of industries — automobile, aeronautic, packaging and pharmaceutical — could use NCC in coatings and materials instead of petrochemicals.
"Because of that, we'd be able to displace the petroleum economy in a variety of ways," says Berry.
However, NCC is not a bio-plastic, he explains. It's an additive that can be easily combined with bio-plastics and conventional petroleum-based plastics. Since it's stronger than steel and lighter than glass, it can strengthen and lighten them dramatically.
"If you look at Obama's 35-mile-per-gallon requirement for new cars, the only way you can do it is with a lightweight structure," says Berry. "If you just use plastics alone, they won't have the rigidity, stiffness and strength needed. But it could be achieved with NCC as the reinforcing element."
The automobile sector has a keen interest in NCC, says Craig Crawford, CEO of the Ontario BioAuto Council, a Guelph-based non-profit. Formed in 2007, the organization represents auto parts makers from various sectors in the emerging bio-based supply chain, and includes major parts assemblers such as Ford and Chrysler. The council is eyeing two key areas for development: more durable coatings and using NCC in composites, instead of steel, to increase fuel efficiency, says Crawford.
NCC can also be combined with the new bio-plastics entering the market. Many of the these new materials developed by major chemicals companies such as Cargill and DuPont from food crops are still works in progress and have many deficiencies that are slowing their uptake. For example, they deteriorate faster in sunlight than petrochemical-based plastics and don't perform well in hot environments.
NCC can correct many of these deficiencies so they perform as well as conventional plastics, says Berry. "Adding NCC can improve bio-plastics in many ways — for example, in meat trays and other food packaging," he says.
Other sectors are also starting to recognize the enormous potential of NCC and other cellulose-based nano-materials. The mining industry could make better use of minerals when they're married with NCC, instead of using more energy-intensive plastics and metals, says Phil Jones, Atlanta-based director of new ventures at mining company Imerys Mineral Ltd.
"We're looking at a materials science revolution using NCC instead of oil-based materials to improve the rigidity of products," says Jones.
Berry says the strategy for commercializing NCC over the next three to five years is to tackle the low-hanging fruit first: penetrating the market for wood coatings, then extending the knowledge gained to coatings and deeper structural elements for other sectors such as the automotive, aeronautical, packaging and pharmaceutical industries.
To facilitate cross-industry development, a new R&D network called ArboraNano was set up this year through Industry Canada's Business-led Networks of Centres of Excellence. The initiative received $8.9 million in funding over four years and is working with industry partners such as Bell Helicopter and Kruger, as well as scientists at McGill and other universities, to develop and test new materials made with NCC for various industries.
Green survival tactics for industry
All of this is good news for Canada's forestry industry. Hard-nosed economic imperatives, not just green goodwill, are driving the battered forestry sector to pour millions into research for new products.
Over the past two years, the Canadian forestry sector lost 50,000 jobs as more than 250 mills closed or suspended operations, according to Avrim Lazar, CEO of the Forest Products Association of Canada.
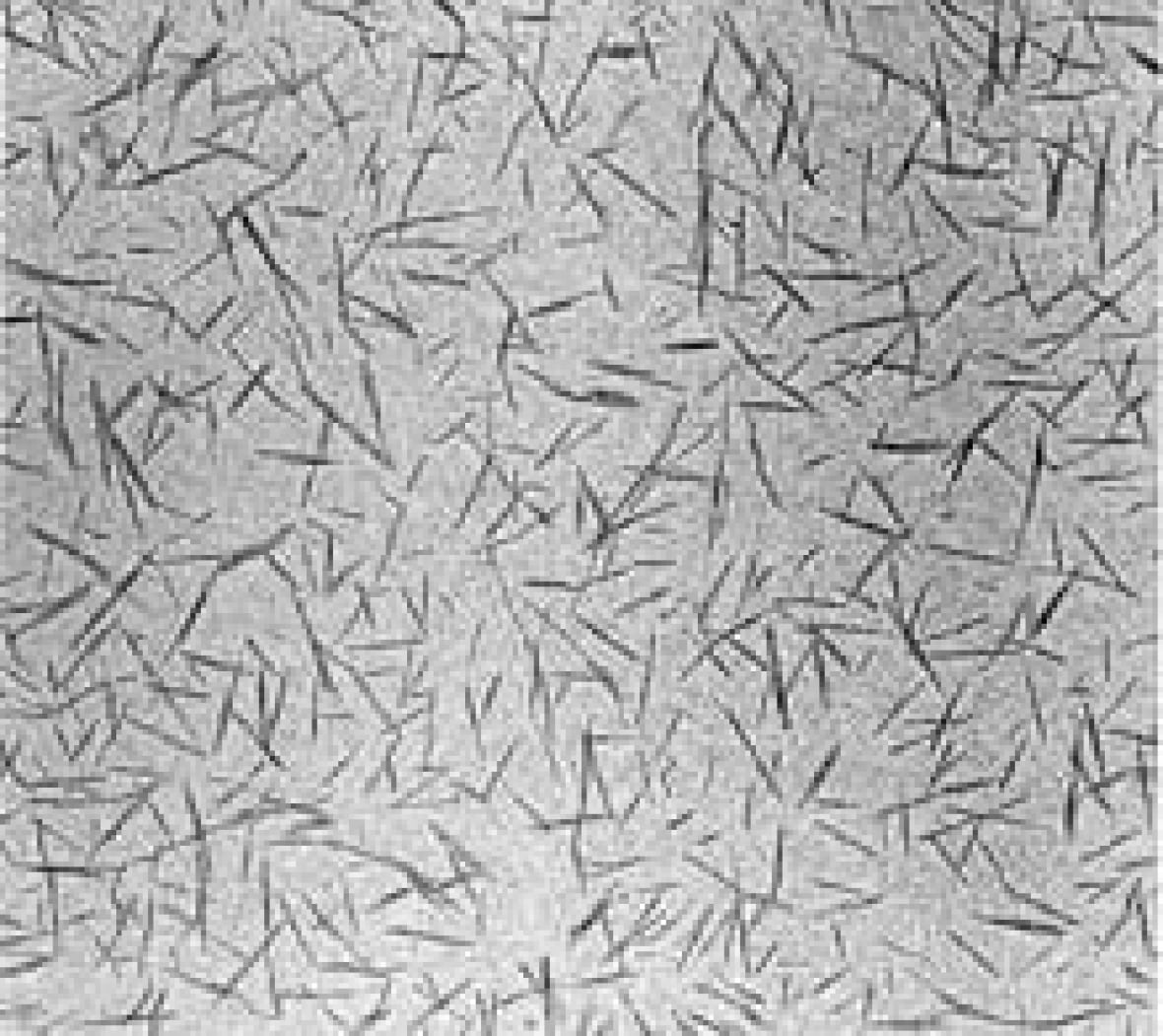
Canada is unique in developing a low-energy chemical, rather than mechanical, process for large-scale production of NCC, he adds.
NCC can be made from any tree or plant cellulose source, says Brian O'Connor, environmental program manager at FP Innovations. "It can even be made from agricultural residues. But there's no existing process in place for that, so you'd need to develop one. The forestry sector already has pulping processes in place that do 98 per cent of the production needed for NCC."
Says Imerys's Jones: "We already have a big chunk of capital on the ground for collecting and processing trees. I hope we don't squander these opportunities by shutting down too many mills and leaving it to other countries to develop them." And are there enough trees in the world to displace petrochemical-based materials with cellulose-based ones?
"Oh yes," says Berry. "They would not consume that much biomass. It's a renewable source and we have a variety of ways to produce the cellulose needed from trees and other plant sources."