Sudbury's tailings ponds could hold key to easing EV battery shortage, researcher says
Metal-eating bacteria could help extract $7B-$10B worth of minerals at Copper Cliff
The key to supplying the automotive industry with enough electric vehicle batteries may rest in a toxic eyesore: Sudbury's vast tailings ponds.
Tailings are the waste material left over from ore extraction processes — often mixed with water and stored in ponds. But for several years, the potential for leaks of toxic substances into the surrounding environment has raised concerns about these tailings and questions about what, if anything, can be done with them.
Nadia Mykytczuk, the interim president/CEO of mining research facility MIRARCO and interim executive director of the Goodman School of Mines, both at Laurentian University in Sudbury, said there's a way to reuse the tailings and provide enough material needed for the expected demand in electric vehicle (EV) batteries.
Mykytczuk, who was Laurentian's Industrial Research Chair in Biomining, Bioremediation and Science Communication, presented her ideas at BEV In-Depth, a major conference on the future of electric vehicles held at Science North in Sudbury on Wednesday and Thursday.
"The challenge ahead of us is that we have to make a very rapid transition away from fossil fuels, and that means we're going to have a very rapid increase in demand for battery minerals," Mykytczuk told CBC News. "We've got to make lots of batteries to drive you to get the electric cars and get them in the hands of consumers.
"And that's going to take a lot more mining."
Biomining could lower cost of extraction
In April, Steve LeVine, editor of The Electric, a publication that focuses on electric vehicles, said in an interview with CBC News that the world's mines produce only about half of the critical minerals necessary to meet the auto industry's EV goals.
This year, he said, automakers plan to build 7.7 million EVs but will only have access to enough nickel — a key ingredient in their batteries — to build about 3.6 million that can travel 400 kilometres or more on a single charge.
"At the end of the decade, the desire is to make between 25 million and 40 million EVs, if you count the Chinese [industry] and Tesla," LeVine said. "There's enough nickel to make 13 million."
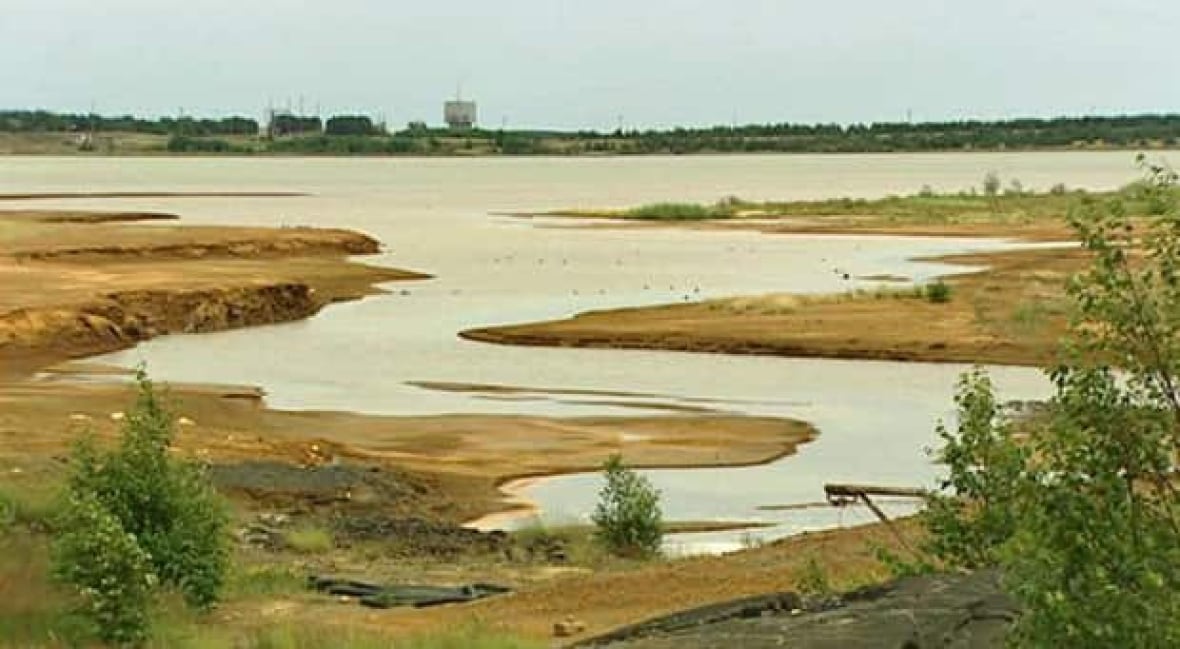
According to Mykytczuk, that's where Sudbury's tailings come in.
"We have a lot of metals actually sitting at the surface contained in mine waste," she said. "If you go to Copper Cliff and the tailings area, which is quite vast, it actually contains a significant amount — between $7 billion and $10 billion worth of nickel sitting in those mine waste."
Despite the estimated value of the waste material, companies haven't yet put money into extracting the metals because of the significant cost of sending the tailings back to smelter, she said. But that could change with the application of bacteria in a niche field called biomining.
"We have diversity of lifeforms on this planet," Mykytczuk said. "These bacteria actually evolved to eat iron and sulphur. They can break down the minerals like pyrite and pyrrhotite that actually carry metals like nickel, copper and cobalt."
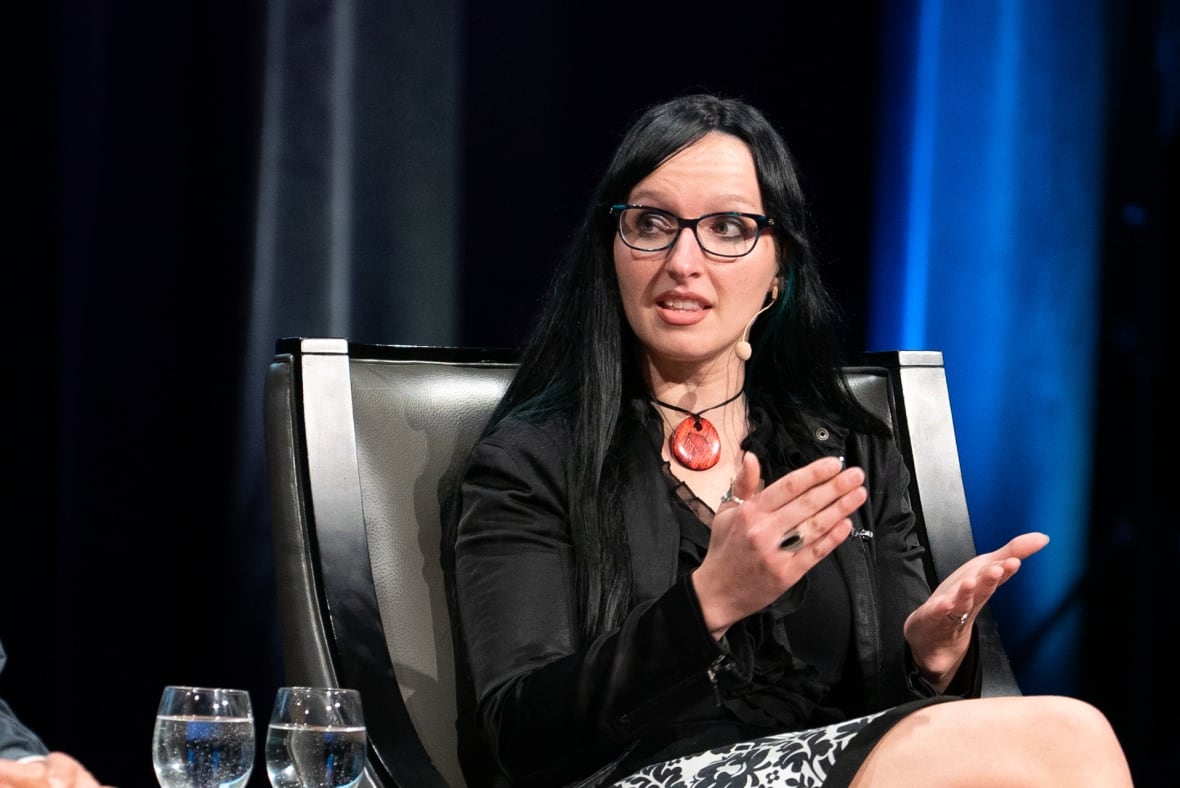
Imagine a brewery, she said, and its large metal tanks used to ferment beer.
"You can build large metal tanks that we call bioreactors, and you can feed the material in," Mykytczuk said. "The tailings are like a fine, sand-like material. We put that into the reactor, we add a few nutrients into the liquid matrix, a bit of acidity.
"We then stir and aerate that mixture and allow the bacteria to break down those materials," she said. "We then separate the solids away from the liquids, and the liquids now contain a concentrated amount of that nickel and copper and cobalt that we're after."
In the past, monitoring this process has been a bit of a "black box," Mykytczuk said. But recent advancements in genome sequencing will allow developers to monitor the activity closer.
"Controlling a biological process, if you're not actually monitoring it, can be very difficult," she said. "It could go one way or the other if the bacteria sort of shift from one community to another.
"But that's all changing," she said. "We're working on making it a reliable and robust technology to tackle these waste materials that aren't going to be economic using other extraction methods."
Ministry responsible for dam safety inspections
In an email to CBC News in November 2021, Ontario's Ministry of Northern Development and Mines said it is responsible for tailings dam safety inspections through its Engineering Services Unit (ESU).
"The ESU undertakes engineering reviews of construction projects for offline tailings structures such as dams (structures not impounding part of a lake, river or stream) at operating mines," the statement said.
"It also conducts site assessments and risk evaluations of abandoned mine tailings dams across the province, to help prioritize repairs at these sites."
In the last 15 years, nickel mining company Vale has upgraded five dams in the Copper Cliff region that were built using what the industry calls the upstream method. That is when the tailings materials themselves — which are the rock waste byproduct of mine milling operations — are used to build a dam.
In 2019, following the collapse of a tailings dam in Brazil, Vale released a review of its tailings dam infrastructure around the world. That report listed eight dams in Copper Cliff that had an "extreme" hazard designation if they were to collapse.
Of those eight dams, four were built with the upstream method.
With files from Morning North and Jonathan Migneault