How yeast and bacteria could be key to future fashion design
'Imagine if you could have a pair of jeans that actually lived and died with you'
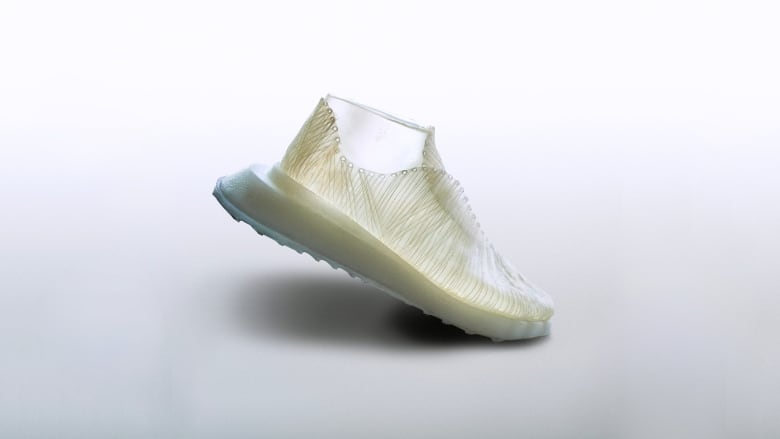
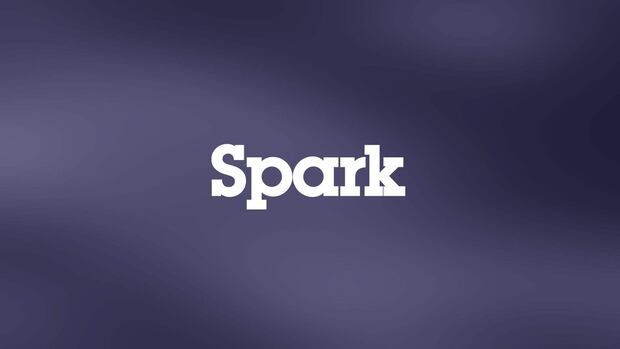
Originally published in May 2023.
In the face of today's resource-hungry garment industry, what if there was a more sustainable alternative, where we could grow our textiles using fungi and bacteria?
That's a scenario researchers have been working to bring to life for years now.
Biofabrication, a process that employs raw organic materials to create products, is being used to design an entirely new class of textiles to displace a lot of the animal and plastic-based textiles and materials we use today. Efforts have largely focused on working with microbes like mycelium, algae and bacteria, to produce naturally occurring polymers like cellulose — a building block of the natural world found in both plants and animals.
"The bacteria that we use was isolated and sequenced from kombucha tea by my co-founder Ben [Reeve], almost a decade ago," Jen Keane, co-founder of Modern Synthesis, a London-based biomaterial company, told Spark host Nora Young. Keane and her team are working to develop a micro-cellulose textile by 'co-creating' with bacteria.
To see how microbial weaving works, click on the video below:
A synthetic culture of bacteria and yeast (SCOBY), a jellified-looking mat, is a byproduct of kombucha that turns sweet tea into kombucha. The bacteria going through the fermentation process converts sugar into tiny fibres called nanocellulose — a lightweight material that is eight times stronger than steel, stiffer than Kevlar, and can bind itself to create fine webs.
During her postgraduate studies, Keane grew the upper of a shoe using this technology. A thread of yarn was fashioned into a pattern to act like scaffolding, which the bacteria grew around to form the end material.
"So you can achieve these really sort of technical synthetic aesthetics, but with a material that is fully cellulosic, so it's fully natural, which means that it could be recycled or is biodegradable," she said.
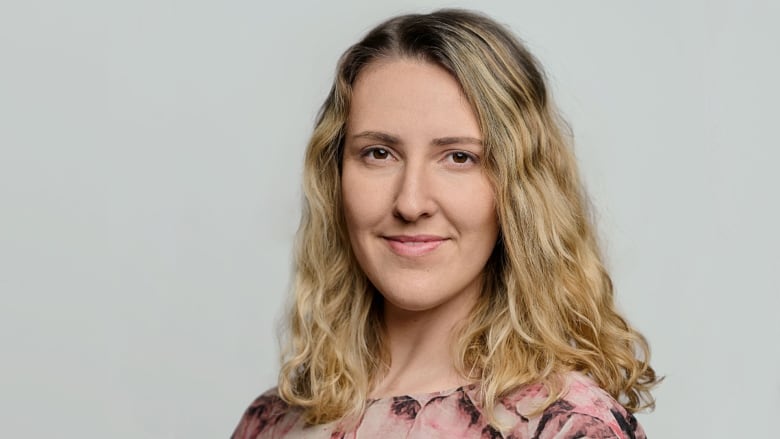
This technology has come a long way since then, she says.
"We've taken that process and we've really looked at scalability and how we can break that down into different parts, [and] utilize existing machinery to form that material in different ways — to make not just one material or one example like this shoe, but actually a whole variety of materials for different applications."
Closing the loop
The use of biomaterials in textiles and apparel isn't novel. It's the cornerstone of a lot of the production already happening. Polyester is derived from petroleum, cotton is mined from the ground.
"But the difference really with this is actually working with biology and working with natural systems and living systems and so that they start to become living factories, factories that are producing materials for us," said Hannah Hansell, an artist and researcher, focusing on the future of the fashion and textile industry.
A few years ago, Hansell created the Living Collection, undergarments made using mycelium with bacteria set within it that's trained to eat sweat and body odour microbes.
The point, she says, was to explore how we could potentially have a symbiotic relationship with bacteria in the future. "But then also the piece was trying to elicit how we would feel about that. Would that be a step too far, that we wouldn't want to have that kind of interaction with microbes?"
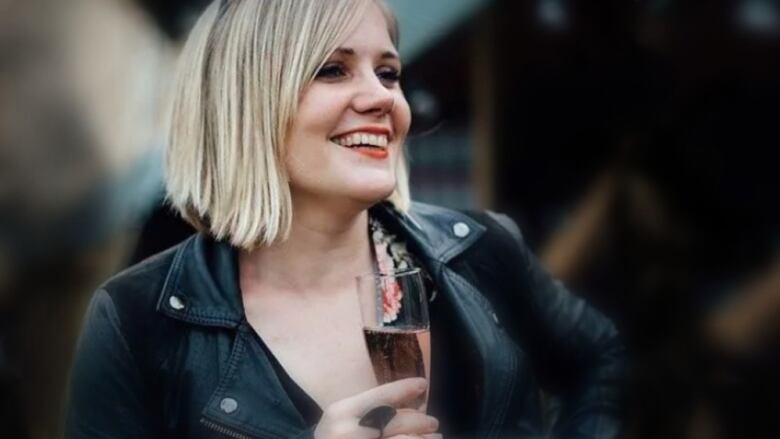
Textiles are the fourth highest pressure category for raw materials and water use. Clothing production alone has doubled over the last two decades. Much of the clothes we don't wear either end up in landfills or are burned — only one per cent is actually recycled.
Hansell says biofabrication offers the opportunity to move away from the linear system of the current fashion industry and condense the production process.
"If you think about something like a cotton T-shirt, you'd be growing cotton on the land. It takes a lot of water use and there's a high pesticide use within cotton. Then it has to be picked, it has to be separated, it has to be cleaned, then spun, before it's even made into a material. And then it gets shipped somewhere else to be made into clothing, then finished, and then shipped again," said Hansell.
"So with the cellulosic based materials, you can even grow them in vats that are shaped into the pattern pieces if you want to."
Through this process, garment makers wouldn't have to make a bolt of cloth and then cut it, rather the cloth would grow into its intended shape. "And in that sense, very much using principles within nature, because nature often will only make what it needs within natural biological systems. It doesn't create waste most of the time. Or byproducts are used in different ways. It's very, very efficient and economical," she said.
Hansell, who made her own individual growth vats, also envisions a material that does not go in the washing machine — but instead, in a nutrient vat where bacteria can mend the fabric as well as clean it.
Weaving the history of textiles
From the Phoenicians' sought-after Tyrian purple dye, to the use of bolts of cloth as currency, textiles have long been linked to status, power and wealth. But Virginia Postrel, author of The Fabric of Civilization: How Textiles Made the World, says that the long history of textiles is also a history of technological innovation — where math, computer science, and cloth weaving converge.
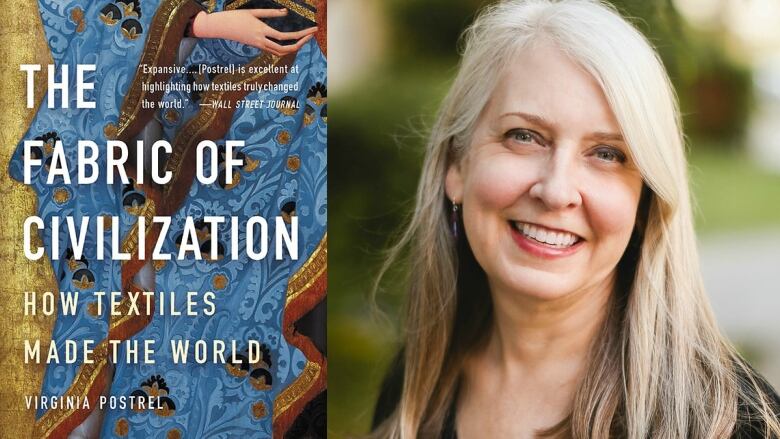
"Weaving, first of all, is the original binary technology. Because a thread is either up or down, you're either going over it or under it. There is a fundamentally binary quality to it," she said.
Frenchman Joseph Marie Jacquard automated the weaving of very complex patterns, which inspired Charles Babbage, who was thinking about early computing, to reflect on how it might work. "Ada Lovelace, who worked with [Babbage], famously wrote that the Analytical Engine would weave algebra the way the Jacquard loom would weave cloth," said Postrel.
In the early history of computing, data was stored on a woven structure of copper wires, called magnetic core memory and had a little magnetic doughnut at the intersection. "And that wasn't modelled on weaving, It just fell out of the essentially binary nature of weaving," she said.
Like computing technology, the mechanics behind garment production have evolved a lot over history, with the shift from plant and animal derived dyes to synthetic ones, and knitting largely eclipsing weaving.
The future of textiles
But when it comes to transitioning to biofabrication, there are concerns around public acceptance.
"I think sometimes when you talk about synthetic biology it can frighten people," said Hansell.
"It can seem quite unknown, the potential of manipulating life, which essentially is what is happening. But a lot of the techniques and processes that are happening are not that far off from things that we've been doing for hundreds of years around cultivation and crossbreeding, how we make beer, how we make kombucha."
Keane says scalability is another roadblock to adopting this technology for mass production. Though bacterial nanocellulose has also been produced at scale for other industries for years, including healthcare and food. "We can tap into not only that knowledge, but also those capacities to scale up quite quickly."
Hansell says there's a need to rethink our relationship with clothes and how we move toward more regenerative production systems.
"Imagine if you could have a pair of jeans that actually lived and died with you. That we started to use things like entropy in the design process. Would we be more connected to our garments and less likely to throw them away, if they had more of a living lifecycle to them rather than being so easily disposable?" she said.
"I see my ideal future as being something where we have potentially these new biological processes that could help to connect us to our clothing more effectively, emotionally and physically."